The restaurant and food industry is finding it difficult to completely eliminate plastic from its single-use items, and from packaging. Now, after years of collaboration, the partners in a BioInnovation project have developed a fully bio-based alternative that can phase out the plastic that has previously been very difficult to replace. The bio-based solution is easy to recycle and is neither more expensive nor more resource-intensive to produce.
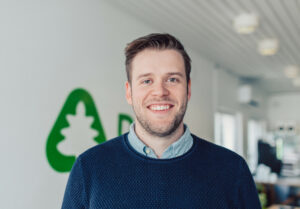
Victor Engdahl, PulPac. Photo: PulPac
For packaging to contain that greasy takeaway burger or a piece of meat in the fridge, the inside is coated with a thin, protective plastic film. In the wake of increased climate awareness, PFAS warnings and the EU Single-Use Plastics Directive, many stakeholders are looking for alternatives to plastic, but this particular protective barrier is very difficult to replace. Now, a BioInnovation project is close to a solution that enables a paper package to store a high-fat food product, for example, without breaking or leaking.
– We are on the track of a solution that can eliminate plastics in much of the single-use packaging and products for foods, that currently rely on a plastic barrier. The collaboration in this project takes us to the next level, for example we could make a completely bio-based fat barrier, says Victor Engdahl, Supply Chain Developer at technology innovation company PulPac, which is leading the BioInnovation project.
Affordability is an absolute must
In the project, the partners have combined innovative chemistry and technology with a new production process. This features the chemical company OrganoClick, which has developed a bio-based barrier solution that can replace plastic. Nordic Barrier Coating makes the barrier workable by applying it to a sort of sheet that is adapted to PulPac’s patented dry moulding process. This involves 3D moulding cellulose-based packaging with minimal water use and with low energy consumption. The technology is offered to packaging producers through licence agreements. PulPac works with machine manufacturers globally, giving producers access to the technology, machines, materials and expertise needed to transition to plastic-free production.
–The goal is a fully bio-based product that can be recycled, that breaks down if it ends up in the environment, and has a competitive price. A reasonable price is an absolute must if we are to replace plastic on a broad front, says Victor Engdahl.
The collaboration began several years ago when, as part of a BioInnovation-funded hypothesis-testing project, the partners succeeded in developing a grease-resistant paper tray. This is a product that is not widely used in Sweden, but globally it is common for fast food to be served on a single-use plastic tray. It remains to be seen what the first commercial product to emerge from this collaboration will be, more large-scale tests will be evaluated first. The performance requirements of the barrier differ depending on whether it is to be used for a takeaway lunch for example, or to store food for several days.
The start of a larger production line
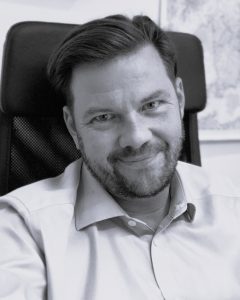
Urban Winberg. Photo: private.
Within the ongoing BioInnovation project, Nordic Barrier Coating has built a pilot machine to produce the barrier sheet that then goes into PulPac’s dry forming process. Now the focus is on optimising the surface layer to which OrganoClick’s chemical barrier solution is applied, so that it works optimally in the next step in PulPac’s process.
– In recent years, we have spent a lot of time developing techniques for applying the barrier. As a relatively small company, it would not have been possible to venture into new territory like this without support from BioInnovation. The pilot machine is the beginning of a larger production line, aiming to produce biobarriers at the same cost and with the same performance as existing plastic products, says Urban Winberg, CEO of Nordic Barrier Coating.
Huge demand for plastic-free barriers
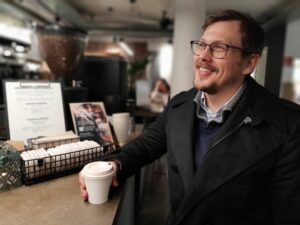
Dan Blomstrand. Photo: OrganoClick
In addition to being bio-based, OrganoClick’s binder is also free from fluorocarbons – an unpleasant chemical in many single-use food items.
– By growing together with Nordic Barrier Coating and our other customers, we look forward to making this a substantial part of our business. We have a turnover of just over SEK 50 million in our business area, and if we get it right this could become a significant part of our business. The demand for this type of new grease-repellent barrier is big, says Dan Blomstrand, Business Development Director at OrganoClick.
- OrganoClick’s barrier solution. Photo: Hans-Erik Nygren.
- Tray with biobased barrier. Photo: Emelie Andersson
- In the lab. Photo: PulPac.
Read more on the project page Development of circular packagings based on the combination of Dry Molded Fiber with bio-based barriers