When a building is demolished, most of the timber goes to incineration in heating plants. What if it were possible to extend the lifetime of some of the wood materials by using them in the facades of new buildings? Industry and researchers are currently exploring how we can increase repurpose timber by enabling new ways of working and collaborating.
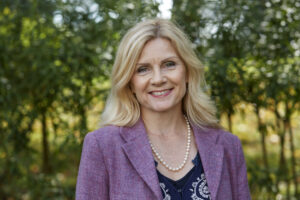
Karin Sandberg, RISE. Photo: Johan Olsson.
– Here we are working with the ”fillets” of the tree trunk, which might be old floorboards or joists, which instead of being thrown on the rubbish heap can be upcycled into new facade elements. What we are testing is something completely new, but it is based on old, proven knowledge, says Karin Sandberg, project manager and senior researcher at RISE.
By ’proven knowledge’, Karin Sandberg means that the project will utilise the same techniques used by sawmills when scanning the surface of juvenile wood to detect knots, cracks and other features that affect the quality of the wood. The researchers will also use computerised tomography to assess the internal quality of the planks, one challenge being that reclaimedtimber often contains nails and other metal objects.
– We want to know which techniques are suitable for mechanically sorting reclaimed material based on quality. But we also want to use AI to understand how much of the material collected can be used when the customer’s requirements for the particular look and feel of the facade are taken into account, says Peter Bomark, a researcher at RISE and participating in the project.
The project also involves conducting a material flow analysis, assessing the availability of the reclaimed material as well as conducting life cycle analyses that can form the foundation for environmental certification.
Ready to use ‘demolition wood’ in the production of new wood products
The pace is fast. The ambition of the project is to produce a facade element that can be used in the Arctic Center of Energy competence centre, currently being built in Skellefteå. The route goes via a new value chain represented by project partners in the form of property owners, construction companies, recyclers and manufacturers of facade elements.
In the project, wood waste from properties demolished by the demolition and machinery company Lotus, will be collected by Ragn-Sells and then transported to RISE, Luleå University of Technology and Norsjö Trä. Together they will embark upon the development of a first prototype:
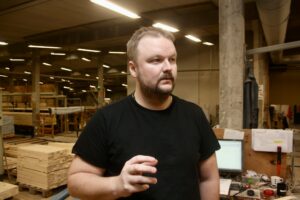
Frank Signarsson. Photo: Lars Westerlund.
– The process itself is already in place. We have previous experience of this, and we are currently investing in a robot specially developed to bring industrial wood waste into our production of wood products for the construction sector, says Frank Signarsson, Production Manager at Norsjö Trä. He continues:
– We need know-how and we have to define the rules of the game that will ensure the availability of reclaimed wood. Only then will making the essential investments in critical steps, such as automated detection and the removal of metal objects from the planks, be justified. This project is a major step towards industrialising the management of old wood in the construction sector.
“It is wise to have started the journey”
Assessing the availability of reclaimed materials is difficult, because in principle it is impossible to identify which buildings are to be demolished, and the quality of the wood residues that will be found. As a first step, Karin Sandberg says it might be possible to mix wood from industrial waste streams with reclaimed wood in the facade materials, in order to guarantee the quantities for large-scale production.
The construction company Lindbäcks in Piteå is another project participant. They build multi story timber buildings through the manufacturing of fully prefabricated modules that are assembled like Lego bricks, directly on site.
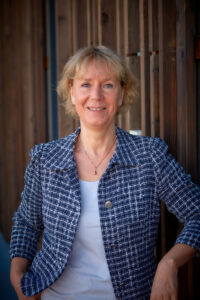
Annica Lindbäck. Photo: Kim Holthe
– The construction sector’s carbon footprint is significant, and there are many efforts underway to make the sector more sustainable. For instance, Boverket– the Swedish National Board of Housing, has been tasked by the government to propose measures that promote circular structures in the future. It’s encouraging to see initiatives aimed at reducing environmental impact and fostering innovation in the construction industry.
I see management of the materials that are already in circulation as an obvious development, and facade materials in particular are a good first step, not least because we continue to bind carbon dioxide that way. It is wise to have started this journey, says Annica Lindbäck, Sustainability Manager at Lindbäcks.
Participants
Research Institutes of Sweden (RISE), Luleå University of Technology, (LTU), Swedish University of Agricultural Sciences (SLU), Norsjö trä AB (Nor), Trä & teknikcollege (T2), PEAB, Lindbäcks Bygg (Lind), Grönbo Produktion, Skebo, Würth, Ragn-Sells Recycling, Snidex, IsoTimber, Lotus Maskin & Transport AB (Lotus) and the municipality of Skellefteå.
Budget & time plan
The project’s total budget is 6,3 MSEK and the project runs for about 2 years – between June 2023 and July 2025.