Only 1% of all the clothing produced is made from recycled textiles. The EU is promoting a more sustainable and circular textile industry, and a newly launched BioInnovation project aims to contribute to this development by offering recycled textile fibres to clothing producers.
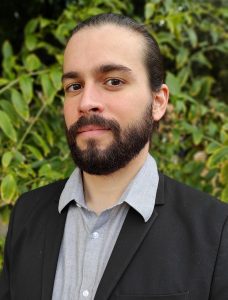
Miguel Sanchis. Photo: ShareTex
The fashion industry is currently transitioning from today’s linear flows towards greater circularity and sustainability. Initiatives at EU level have resulted in a legal requirement to collect household textiles separately from 2025, much as we do with cardboard boxes and newspapers. As it becomes easier to collect textiles, the need to find ways to recycle them also becomes apparent.
– The textiles that are recycled today are primarily used for other, lower-value products such as additional insulation. There are limited methods for recycling textiles into new fibres that can go back into textile production. To reduce this huge waste of resources, more expertise and new processes for textile recycling are needed, says Miguel Sanchis, CEO of ShareTex.
New process can increase the proportion of recycled textiles in clothing
ShareTex has developed a process that recycles high quality fibres, allowing a textile fibre such as cotton to be circulated several times. This can be compared to the processes that exist for textile recycling today, where the cotton fibres are recycled directly into viscose. And once the viscose is worn out, it cannot be made into new textiles again.
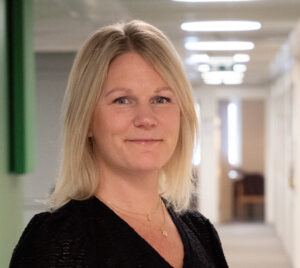
Sofia Bylund. Photo: Henik Högberg.
With the actual recycling method in place, ShareTex will now be making the recycled fibres suitable for textile producers. Within the framework of a newly launched BioInnovation project, the goal is to develop a technique for spinning the fibres into threads that can subsequently go back into textile production. The spinning process is being developed together with RISE and Lund University, and the machine manufacturer Valmet is researching which machines are suitable for the task.
– The well-established technology and know-how we already have from the paper and pulp industry can also be applied to textile fibre processes. We are currently investing in technological development, and we are using our pilot facilities to develop processes for textile fibres in collaboration with both customers and partners, says Sofia Bylund, Manager process engineering within the Fiber processing business, Valmet.
H&M: “The circular aspect is extremely important”
H&M is also involved in the project. They provide support, among other things by comparing what is produced from the recycled thread with existing materials, in order to ensure that the recycled textile is suitable for different commercial purposes.
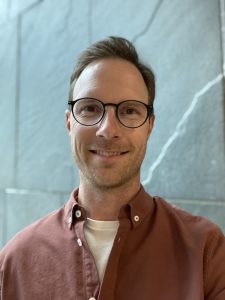
Neal Fernandez. Photo: Private
– By being present as a support function in early projects, and later on making our supply chain available, we can speed up the implementation of more sustainable materials. The idea is that we, as well as many more industry stakeholders, will benefit from the innovations we are supporting. This is the only way that production will be able to reach sufficient large-scale volumes that the transition to circular and more sustainable materials can happen on a broad front, says Neal Fernandez, Project Manager, H&M Circular Innovation Lab:
– The circular aspect is extremely important. We need to utilise the materials that are already on the market and break away from the linear flow that dominates today.
When the project ends in 2024, it will demonstrate the entire process at lab level.
– Hopefully, this project will bring us one step closer to a feasible circular value chain in the textile sector, Miguel concludes.
- On the left, textile waste that comes in to ShareTex, on the right, recycled cellulose pulp. Photo: Sharetex
- The textile waste is dissolved… Photo: ShareTex
- … and is spun into fibres. Photo: RISE
- The result: 100% recycled fibres. Photo: RISE
Participants
ShareTex AB, Valmet AB, H&M Hennes & Mauritz GBC AB, RISE AB and Lund University Dept. of Chemical Engineering.
Budget & time plan
The project’s total budget is 2 MSEK and the project runs for two years – between November 2022 and November 2024.