Cross-laminated timber (CLT) has paved the way for more competitive timber construction with a lower carbon footprint. Currently, cross-laminated timber panels are installed with screws – a time-consuming procedure that also makes future reuse more difficult. A BioInnovation project is developing a screw-free solution inspired by click flooring.
The construction and real estate sector accounts for more than 20% of Sweden’s climate impact, and using more wood in construction is one way of reducing the sector’s emissions. Cross-laminated timber (CLT) has an important role to play here, in part because its high strength and low weight means it can replace steel and concrete.
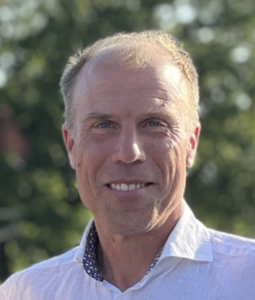
Marcus Bergelin, Moditri. Photo: David Elmlund
To make wooden house construction even more competitive and to reduce climate impact, a BioInnovation project aims to eliminate the large volumes of screws used in the assembly of CLT panels – with a particular focus on floor slabs. The project is being led by Moditri, which has developed a patented joining technology called XLoc™️, where the CLT boards are clicked into place just like with a modern parquet floor. The innovation can phase out steel, as well as a time-consuming and labour-intensive operations, which today may cause repetitive strain injuries, on the construction site.
– Click flooring has revolutionised the flooring industry and I believe we will see the same development in house building. Screwless construction solutions provide many positive effects, each one of them alone being a sufficient reason to introduce the technology, says Marcus Bergelin, CEO of Moditri.
Testing live, on a building in Umeå
The stability of a building is influenced by how well each part of the structure is assembled. This type of joining technique can increase safety by removing the risks associated with incorrectly installed screws. It creates the conditions for circularity and helps increase the added value of cross-laminated timber panels, as they become significantly easier to reuse.
Within the BioInnovation project, the first industrial panels have been developed and Martinsons, the project partner, together with AR Bygg installed the floor slabs in a building in Umeå. These were then compared with current materials and methods.
– The positive effect on construction costs, on the climate and on the workplace environment makes this a prioritised project, fully in line with our efforts to increase the construction of wooden buildings, and to find ways to use wood more efficiently. According to our calculations and the tests carried out so far, this is a promising innovation, says Gunnar Lundmark, Quality and Development Manager at Martinsons.
‘A very realistic start’
The evaluations and tests carried out to date show that the screwless CLT panels can be manufactured using existing machinery, and that the marginal cost increase that comes with providing the panels with splices is recouped through a more efficient construction process.
– Ultimately, we could click entire buildings together, but focusing on the floor joists themselves is a completely realistic beginning, that doesn’t require major changes to the industry and doesn’t add complexity to the construction. Now we are getting the ball rolling by starting to use the innovation, and by collecting data that shows the benefits, says Marcus Bergelin.
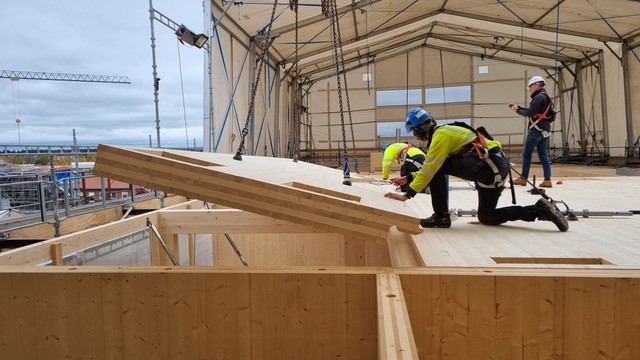
The installation in Umeå. Photo: David Elmlund.
We followed up with Marcus Bergelin again in March 2025 on the installation in Umeå.
– The installation is complete, and the results surpassed our expectations. Martinsons delivered the material and AR Bygg completed two identical installations on different floors of a building in central Umeå; one with traditional screwing and one with XLoc™️, so that we could compare like with like. It was a bit unfair as there we had a technique that the installers were familiar with after many construction projects using screwing, being compared with clicks used for the first time ever. The fact that we got a very good result under such conditions is a strong statement how good the technology is. It usually doesn’t go so well the first time you do something, says Marcus Bergelin continuing;
– Among other things, we saw that the lead time during the installation phase was reduced by more than 50 per cent, and the time spent per installed panel was reduced by more than 60 per cent. This freed up resources in the construction team, allowing those people to carry out other tasks. The potential is probably even higher because the construction crane is used to having plenty of time during floor installations. Now they suddenly became a bottleneck, and they were not ready to streamline their work in order to keep up.
Read more on the project pages:
Resource efficient bio-based interlocking of CLT – step 1