A wooden high-rise residential area is currently being built in Mariestad. To reduce vertical deformations caused by the load of the multiple storeys, the construction project is testing a new kind of rail, made from a by-product of the production of cross-laminated timber. The rail can substantially reduce the settling often suffered by high-rise wooden buildings, and give a major boost to modern timber construction.
Wooden house building is all the rage. Building tall, and largely in wood, can be one tactic for meeting climate targets, and can increase the use of circular, renewable materials. One efficient building method is to assemble modules, prefabricated from sheathed timber frames, in a factory. But the taller the buildings that are built in this way, the greater the loads and the risk of settling which can cause problems. To date, this challenge has made it difficult to build tall structures with prefabricated wooden modules. The Achilles heel is primarily the load-bearing parts of the frame, that are called rails and top plates. They contribute to a stable structure, but because they are placed horizontally, they are subjected to loads across the direction of the fibres. This is a loading that usually involves significantly greater deformations than if the load goes along the direction of the fibres.
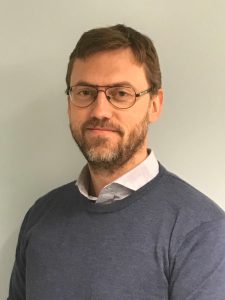
Johan Vessby, Karlstad University.
Now, researchers Johan Vessby and Mikael Perstorper at Karlstad University have found a potential solution. In a BioInnovation project, they have tested and confirmed that a by-product from the production of cross-laminated timber (CLT) has great potential to replace structural timber in rails and horizontal bands. Cross-laminated timber rails meet high stiffness and strength requirements, whilst at the same time being as light as regular structural timber.
– High-rise building in wood with prefabricated modules is becoming more common, precisely because it is so efficient. But it comes with limitations. At around five storeys and above, there is a risk of settling problems that complicate construction and make it more expensive. Now we’ve found a solution; we saw up the pieces left over from the production of CLT and use them to make rails and horizontal bands. The benefits are twofold: firstly, we use a by-product that usually goes directly to energy recovery, and secondly, we can significantly reduce vertical settling in the construction of wooden high-rise buildings, says Johan Vessby.
Half the deformation
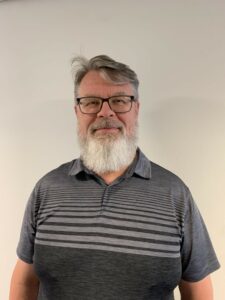
Peter Erlandsson, Vida Building. Photo: Vida Building
Small-scale tests carried out in the BioInnovation project show that the structure is up to five times stronger with CLT-rails, and a long-term field test showed that the deformations were halved in comparison to conventional rails. The CLT-rail is now being tested in six-storey house in Mariestad. The house is being built by Vida Building, one of the partners in the BioInnovation project, and will be one of six identical modular high-rise buildings. The other houses are being built in conventional materials, so the settlements in the house with the CLT-rail can be compared to those in a ‘standard building’.
– Based on the data we have obtained so far, the CLT-rail feels incredibly promising and reliable to use. The CLT-rail is particularly interesting precisely because it is a by-product that is given a higher value in this context, which means that we can build more sustainably. The CLT-rails also facilitate production. As a material they are convenient to build with, and for a company of our size they can easily be incorporated into existing processes, says Peter Erlandsson, Technology and KMA Manager, Vida Building.
Aiming to increase the value of by-products from CLT wood production
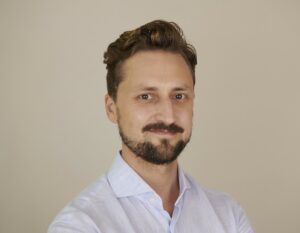
Jacob Eriksson, Stora Enso. Photo: Stora Enso
The BioInnovation project has broad support, the timber house manufacturers Obos, Derome and the CLT producer Stora Enso being involved. When Stora Enso produces customised products from CLT, by-products are generated that are often recycled for energy at present.
– We are constantly looking for ways to add value to our by-products. While energy recovery is good, this kind of long-lasting product which continues to sequester carbon, is even better. Now we have very successfully tested a specific standard thickness to make the rails. In order to reach large-scale volumes, the next step is to use more elements of the standard range from the production of CLT, says Jacob Eriksson, Product Manager Renewable Building Elements at Stora Enso:
– By publicising this kind of research demonstrating good results, we can help make recycled materials a more natural element in the construction industry. I believe this product will be useful in many future applications.
- Timber house modules. Photo: Vida Building
- CL rail. Photo: VidaBuilding
- Close-up on cut CL-timber. Photo: Stora Enso
- Apartment block in Mariestad. Illustration: Arkimark.
Read more on the project page High performing rails from CLT panel waste for advanced prefabricated volumetric timber structures – step 2.